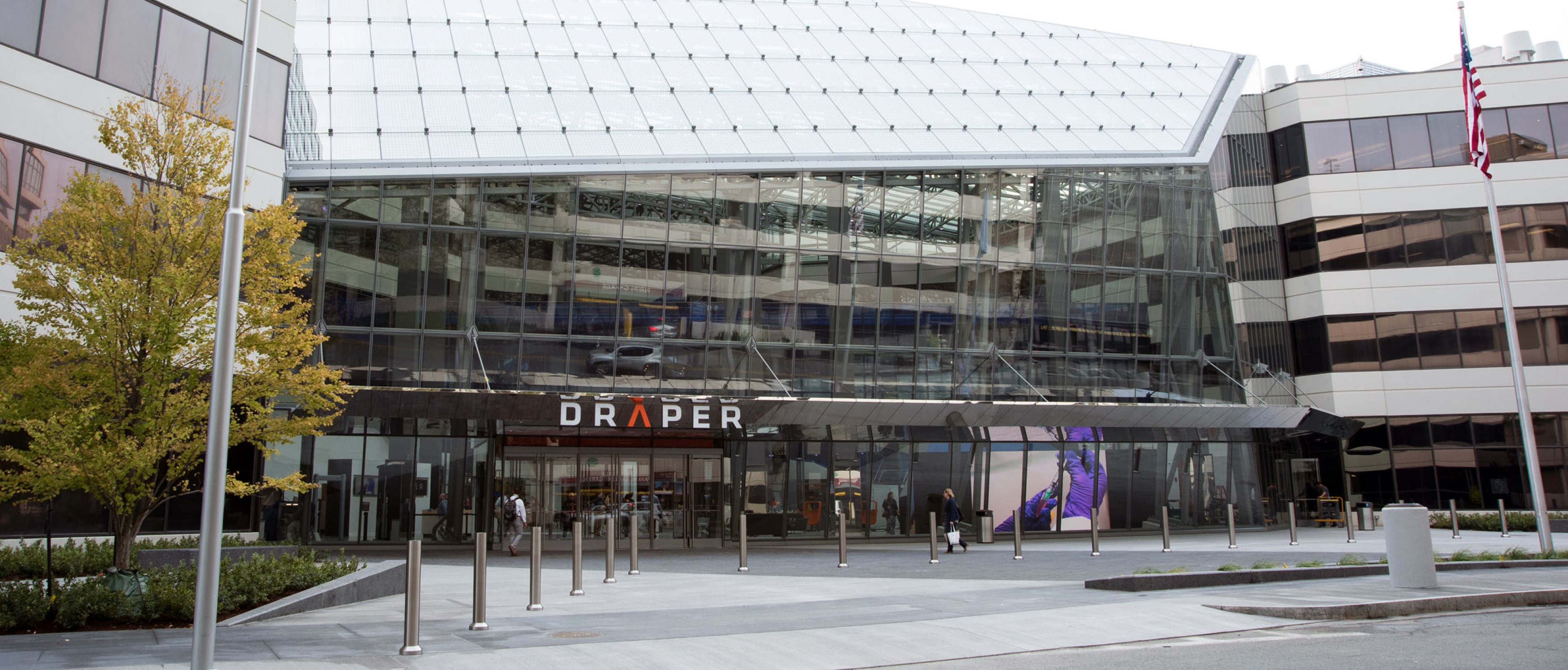
The Draper Impact
Doc Draper used to describe his laboratory by saying, “We make things that work.” He is remembered for advancing the theory of inertial navigation, but even more so for driving its implementation—making it work in the real world. The practical benefit of what he and his team invented was what he cared about. He wanted the technology advancement to make an impact for the user. Looking back over the decades, the work of Doc and his team enabled technology we take for granted now.
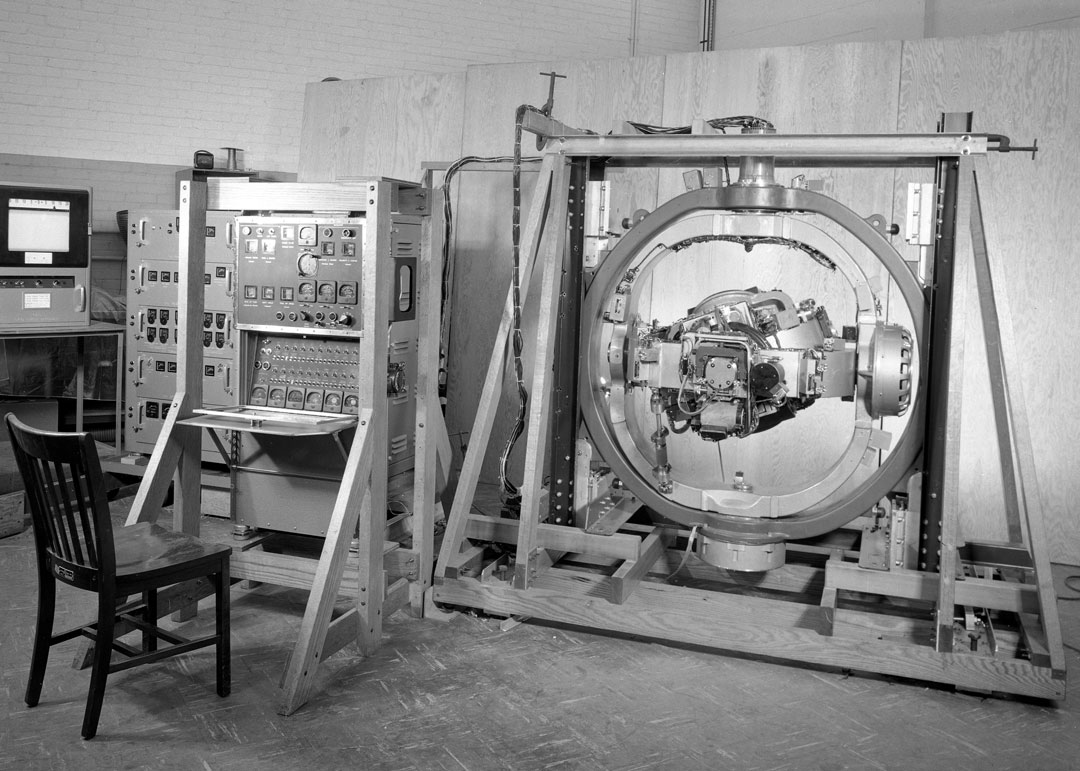
The innovation of inertial navigation technology permeates the world today. Doc Draper wanted the ability to fly using instruments rather than be grounded when visibility was poor. His pioneering work in inertial navigation sprang from his personal passion for flying and his drive to make the technology practical. In 1953 he flew from Massachusetts to California in a B-29 guided by Spire Inertial Reference Equipment, the first cross-country demonstration flight of inertial navigation technology. SPIRE was the forerunner for the autopilot systems used routinely in today’s commercial aircraft.
In the 1950s he and his team began applying inertial navigation to ballistic missiles for the Air Force and then to ballistic missiles launched from undersea for the Navy. Draper also began developing inertial navigation technology for submarines.
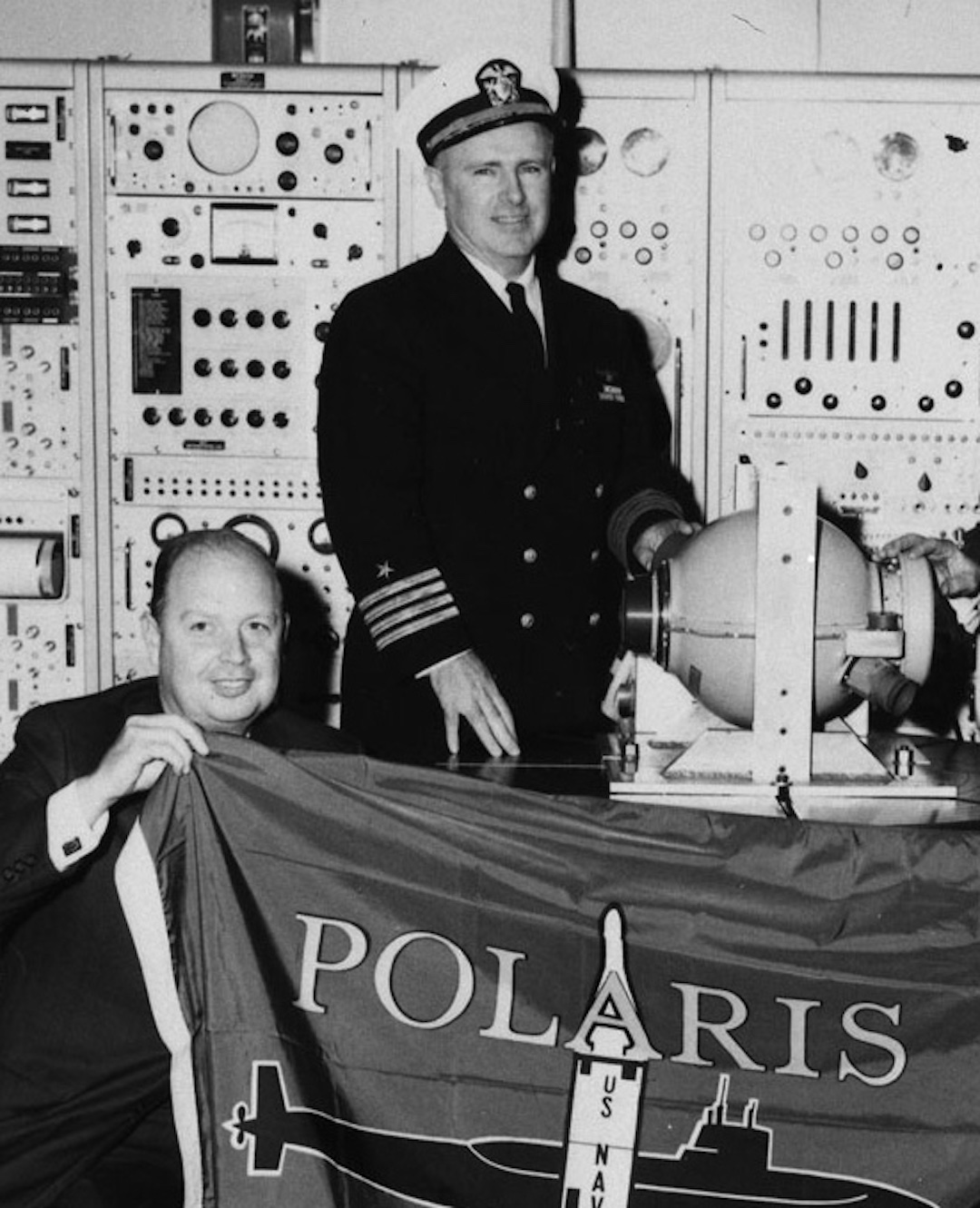
In the 1960s his engineers designed inertial-based guidance and control systems for NASA’s Apollo spacecraft, leveraging work done for the Navy’s Polaris ballistic missile guidance system. Implementing inertial navigation in space required Draper’s team to innovate other technologies, notably the Apollo Guidance Computer—a real-time digital computer and its associated software. Evolved from previous digital computer design work for a Mars probe several years earlier, an Apollo Guidance Computer innovation was use of integrated circuits for its erasable memory. Apollo’s Lunar Module (LM) flew via the Draper-designed Primary Guidance, Navigation and Control System, which ran on the lunar module’s digital computer—the first digital fly-by-wire (DFBW) system developed, used to land the LM on the moon in 1969.
That DFBW technology was later adapted by Draper and NASA Dryden’s Flight Research Center for aircraft, replacing hydraulics, cables, rods and pulleys with digital computer commands and electromechanical actuators to control aerodynamic surfaces. The F-8 aircraft DFBW implementation was triplex fault-tolerant, meaning there were computers working simultaneously and synchronously to ensure reliability. The system was first flown in 1972 and was the forerunner of DFBW systems in use on commercial and military aircraft today.
To miniaturize inertial instruments and systems for use on guided munitions, Draper in the 1980s started exploring microelectromechanical systems (MEMS) technology and adapted manufacturing technology from the semiconductor industry. Draper became a pioneer of MEMS technology. In 1987, Draper’s MEMS gyro based on a vibrating pendulum design, etched from a silicon wafer, was the world’s first to sense angular rate. The first monolithic silicon gyro based on a Tuning-Fork design was demonstrated in 1991. Draper went on to apply MEMS technology to automotive skid control, precision timing, microphones, guided munitions, and chemical and biological sensors, and leveraged advances in MEMS to pioneer microfluidics technologies for tissue engineering, organ on a chip and cell bioprocessing. In 2022 Draper delivered preclinical units of three bioprocessing modules – acoustic separation, electroporation and viral transduction – to a pharmaceutical company to improve its CAR-T manufacturing process.
The company named after Doc Draper carries forward that legacy of technology innovation for impact. We develop and demonstrate effective technology solutions in strategic deterrence, electronic systems, space system and biotechnology systems for our nation as it defends and supports democracy at home and abroad.